Gill Dando, Principal Consultant, RQA Group
One of the things that drew my attention when deciding to join the team at the RQA Group was a highly insightful article written by the company MD, Vince Shiers, on the ‘Never Events’ principle[1]. This principle comes from the surgical profession initially, whereby mistakes on the operating table falling under the guise of “human error” are looked at with a view that they should never occur[2]. So when they do, they are logged and measured as a Never Event. I mean, nobody wants to have to get a follow-up surgery when the consultant realises they lost a pair of forceps, or you wake up and they operated on the wrong leg right…?! Inspirationally, RQA Group has extrapolated this principle to preventable incidents or mistakes that should never occur in the production and processing of food. These ‘Never Events’ are critical incidents that can have severe consequences for public health, brand reputation, and regulatory compliance. When I saw that the MD of the company had this proactive, risk management ethos at the core of the business model I knew this was the place for me.
I have both worked on and seen recalls and withdrawals where it is clear that simple control measures or better knowledge would have easily (and cost-effectively) prevented them from occurring. These could definitely fit the model for being classified as ‘Never Events’, and are often the non-conformances which are put down in a RCA log as “operator error” or “human error”, etc. If you sit back and think about what this means and really scrutinise it, though, is that the true root cause? I would challenge this wholeheartedly. Back in my early career working in sterile injectables (pharmaceutical vaccines), I had an amazing quality manager who would simply not allow terms such as operator error to be a root cause unless it could categorically be shown that this was malicious or intentional. Even then, the jury is out as to whether this is the true root cause or not.
Root Cause Analysis
So let’s think about this rationally…If we take two of the most common and simple root cause analysis (RCA) tools that are out there that almost everyone will be familiar with, the ‘5 Whys’ and Ishikawa (fishbone) diagrams (see above template). The 5 Whys and Ishikawa methods are problem-solving techniques commonly used in quality management to identify and address the root causes of issues or incidents in a systematic manner. The 5 Whys method involves repeatedly asking “why” to uncover the underlying causes of a problem, while the Ishikawa / fishbone diagram, visually maps out potential causes of an issue in different categories.
Operator error, although it may be a contributing factor, is typically not considered a true root cause in these methods. This is because operator error is often a symptom or a surface-level observation, rather than an actual underlying cause. The 5 Whys and Ishikawa methods aim to identify deeper, systemic causes that may be related to factors such as process design, training, communication, equipment, or other environmental or organisational factors. Some examples I have seen time and time again would be things like the operator putting the wrong code in the date coder. Is this really operator error or were they not trained sufficiently? Were they hurried due to production pressures? Could a poke-yoke system help minimise number blindness on a night-shift? Most of these issues could be resolved using technology and coding systems or reassessing genuine production capacity, and it is highly unlikely that the operator purposefully inputted the wrong code. Even if it was intentional or even malicious, why would that be? How do you measure quality culture? Are staff happy in the workplace and do they feel valued? If not, then what steps has the senior management committed to for change? (Is anyone else hearing the updated GFSI and BRCGS version 9 standard principles echo here!)? So as we can see, simply blaming operator error as the sole root cause can lead to a narrow and superficial understanding of the issue, and may result in inadequate or ineffective corrective actions that do not address the underlying causes of the problem. Therefore, without the use of, or indeed improper use of, the 5 Whys and Ishikawa methods (or others), we tend to encounter recurring issues and a proliferation of ‘Never Events’ in the manufacturing and retail space.
What does the data tell us?
RQA Group collates data from different agencies around the globe and aims to categorise and demystify as much as possible to provide meaningful insights for us to work with as consultants, and to offer valuable information for the manufacturing, retail, and product recall insurance industries. We have separate metrics for what are clearly ‘Never Events’ as part of this process, and we observe that a significant proportion of recalls (around 50%) and incidents globally could be completely eradicated with more focus on this topic. Some of these events could be catastrophic, and as we see year on year increases within the allergen sector, it really is time we sat up collectively and address these head on[3]. Our approach to the ‘Never Events’ principle involves designing and implementing proactive risk assessments, robust quality assurance processes, and comprehensive training programs to prevent and mitigate the occurrence of such events in food manufacturing operations[4].
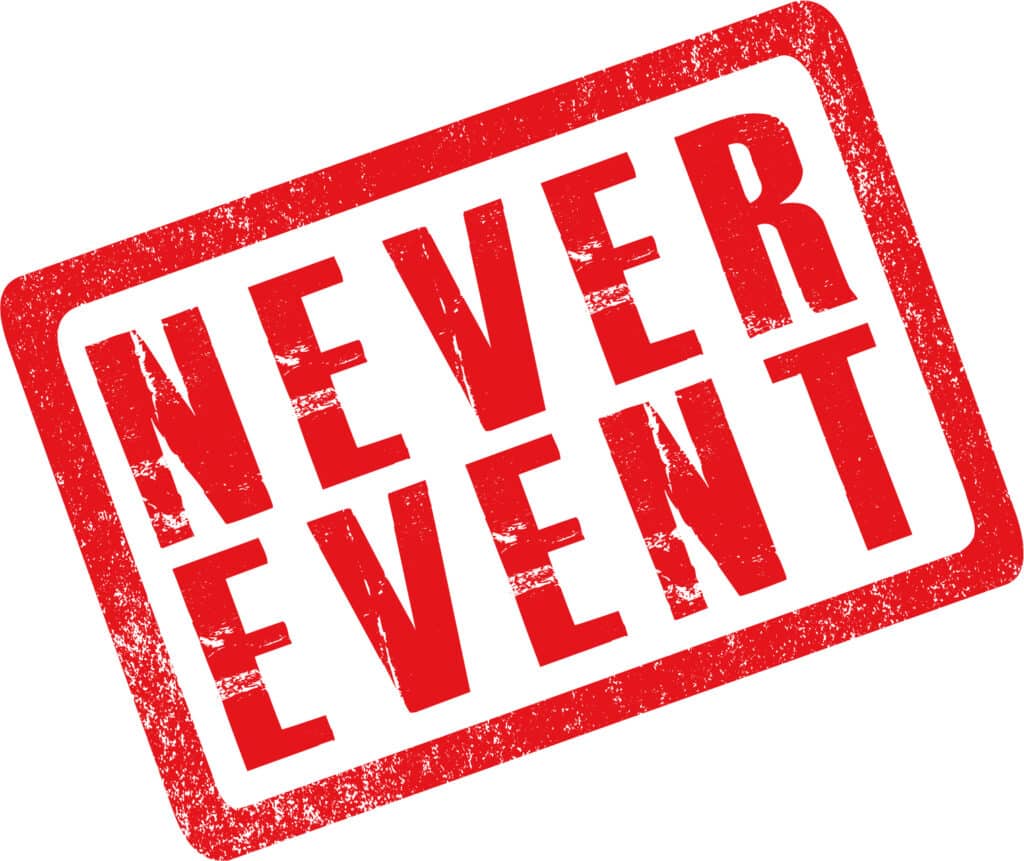
In summary, I cannot emphasise enough the importance of considering, measuring, and tracking ‘Never Events’ within your organisation. RQA Group’s emphasis on the ‘Never Events’ principle and its significance in ensuring safe and high-quality production drives positive culture rewards with limitless benefits. Organisations can take steps to minimise the risk of ‘Never Events’ in food manufacturing or any other industry. It is crucial to foster a positive culture of accountability, continuous improvement, trust, and create a safe space to learn from mistakes. By doing so, we can all strive towards preventing ‘Never Events’ and ensuring safe and high-quality operations. Remember, the key lies in addressing the true root causes and taking appropriate measures to prevent recurrence, ultimately safeguarding public health, brand reputation, regulatory compliance, and the lifespan of the business/product(s).
RQA Group can assist with any of the topics discussed in this article and much more. For more information on our product recall services click here, or get in touch by email on [email protected] or call +44 (0)118 405 0192
RQA Group Principal Consultant Gill Dando has spent over 20 years working in manufacturing (e.g. Greencore, Glanbia, Quorn, Huntsman, MedImmune) and retail roles (Sainsbury’s and Asda) both within the UK and globally. She has a wealth of experience in providing collaborative product safety, quality and technical consultancy to a range of industries. Gill is a trained scientist, has a degree in Biological Sciences with Agriculture & Food Science, and spent a number of years post-graduation in molecular biology and biochemistry laboratory placements focussing on genetic manipulation of microbes and fermentation design in both the food & drug arenas.
[1] RQA-Group-Never-Events-Article-1.pdf
[2] Never Events | PSNet (ahrq.gov)
[3] Preventing allergen recalls by avoiding ‘Never Events’ – Allergen Bureau
[4] RQA-Group-Half-Recalls-Preventable-Never-Events-Aug21.pdf